Welcome, Guest |
You have to register before you can post on our site.
|
Forum Statistics |
» Members: 53,715
» Latest member: Swig4646
» Forum threads: 68,124
» Forum posts: 1,054,665
Full Statistics
|
|
|
SOLD PRICE REDUCED FS: Ryobi Oscillating Spindle Sander |
Posted by: Rick_B - 10-18-2024, 09:50 AM - Forum: Tool Swap N' Sell
- Replies (6)
|
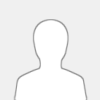 |
OSS IS SOLD
Price reduced to $150 for all
Machines run great – I replaced it with a more vintage machine. Includes all 6 spindles and matching table inserts, a variety of abrasive sleeves in several grits, a rolling stand with storage drawers and a shop vac for dust collection. Dust collection works very well.
I’m asking $175 - $125 for just the machine (no stand or vacuum). Reasonable offers are welcome.
Pictures available upon request
Rick
|
|
|
Spindle Sander suggestions |
Posted by: castguy2003 - 10-17-2024, 08:36 PM - Forum: Woodworking Power Tools
- Replies (18)
|
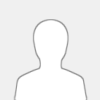 |
My Delta Boss spindle sander motor died in the middle of a project. New motors are not available anywhere. A quick trip to Harbor Freight for their cheap tool got me through the project but that machine is a piece of crap. Any suggestions on a reasonably priced replacement, Jet, Grizzly?
|
|
|
Need some thoughts from the finishing braintrust |
Posted by: doobes - 10-17-2024, 02:23 PM - Forum: Finishing
- Replies (10)
|
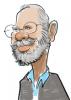 |
Hai der!
I promised my Daughter I would clean up a school house bench she bought at an antique store.
This is what it looked like before I started:
![[Image: Workbench.001.jpg]](https://dubea.com/fotos/workbench/Workbench.001.jpg)
![[Image: Workbench.002.jpg]](https://dubea.com/fotos/workbench/Workbench.002.jpg)
![[Image: Workbench.003.jpg]](https://dubea.com/fotos/workbench/Workbench.003.jpg)
![[Image: Workbench.004.jpg]](https://dubea.com/fotos/workbench/Workbench.004.jpg)
![[Image: Workbench.009.jpg]](https://dubea.com/fotos/workbench/Workbench.009.jpg)
![[Image: Workbench.010.jpg]](https://dubea.com/fotos/workbench/Workbench.010.jpg)
![[Image: Workbench.011.jpg]](https://dubea.com/fotos/workbench/Workbench.011.jpg)
Pretty gruesome, right? It looks like it had been in a fire, and then some miscreant "repaired" it by shoving shavings into the cracks caused by expansion and then "refinishing".
So I got it all apart and started sanding it. The top is Poplar as can be seen from the nice green tint:
![[Image: Workbench.011.jpg]](https://dubea.com/fotos/workbench/Workbench.011.jpg)
It's also interesting as it had been slitted to deal with expansion, but unfortunately as we saw, that failed miserably.
![[Image: Workbench.019.jpg]](https://dubea.com/fotos/workbench/Workbench.019.jpg)
So talking to my daughter, I ripped through the slits with my bandsaw, and then ripped through the splits, cleaned up all the edges and glued the top back together,
![[Image: Workbench.031.jpg]](https://dubea.com/fotos/workbench/Workbench.031.jpg)
This took about 2" out of the width. I've sanded about as much as I'm going to as the top is not particularly thick and sanding isn't helping that.
![[Image: Workbench.032.jpg]](https://dubea.com/fotos/workbench/Workbench.032.jpg)
All the screw hole had been wallow out over the years, so I got a piece of poplar and drilled the holes and plugged them with plugs in the correct grain orientation.
![[Image: Workbench.039.jpg]](https://dubea.com/fotos/workbench/Workbench.039.jpg)
This is what the legs look like:
![[Image: Workbench.042.jpg]](https://dubea.com/fotos/workbench/Workbench.042.jpg)
![[Image: Workbench.014.jpg]](https://dubea.com/fotos/workbench/Workbench.014.jpg)
![[Image: Workbench.043.jpg]](https://dubea.com/fotos/workbench/Workbench.043.jpg)
![[Image: Workbench.045.jpg]](https://dubea.com/fotos/workbench/Workbench.045.jpg)
They were split as well, and burned, and rotted from sitting in water.
The cleats for the underside, I shortened to suite the narrower top and slotted all the holes to allow movement after they are installed:
![[Image: Workbench.046.jpg]](https://dubea.com/fotos/workbench/Workbench.046.jpg)
![[Image: Workbench.047.jpg]](https://dubea.com/fotos/workbench/Workbench.047.jpg)
Now to the gist of the question, what finish to put on it. I asked my daughter and she said "oh just put some tongue oil on it"...
I've never finished Poplar as furniture before.
I'd love to even out the color, and downplay the green tint and then put a topcoat that will protect the soft Poplar.
Please weigh in with your thoughts. I've got a gazillion hours cleaning this thing up and don't want to bugger it up with the wrong finish.
cheers,
|
|
|
Problem with DeWalt drill |
Posted by: Randy C - 10-17-2024, 09:42 AM - Forum: Woodworking Power Tools
- Replies (1)
|
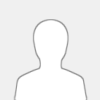 |
I have a DeWalt 20 volt drill that’s about 10 years old. Lately I have noticed that it sometimes will lose power (even when not under a load) and will hesitate and then it will catch back up and run full speed. Does anyone know if this could possibly be a problem with brushes and if so is this something that I could replace?
Thanks
|
|
|
Owl drill bits |
Posted by: tablesawtom - 10-17-2024, 08:55 AM - Forum: Woodworking Power Tools
- Replies (8)
|
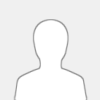 |
I was watching Stumpy Nubs on You Tube the other night. Trust me, I take all you tubers with a grain of salt. Anyway he gave a recommendation about how well Owl bits worked and they somehow didn't have much if any blow out at the bottom of the hole
Well, I have to drill several holes by hand through the top of the work bench I am building. Anyway I checked out Amazon and I found an Owl 3/4 inch bit and the advertisement read developed for battery operated drills. So I bought one.
In a drill press it drills as clean a hole as any forester bit and is a lot easier to line up. Drills a lot fasted with less heat. Drilling through 4 inches of Ash with a 3/4 drill drill bit in a hand drill is not fun, but the Owl bit did it quite easily. Once a person gets so deep chip ejection became a problem and the drill has to be remover about every 1/2 inch for chip removal.
I do not impress easily but the owl bits impressed me enough to order a set of 7, 3/8ths through 1 1/4. They will replace the forstner bits of that size in my shop.
I thought I would pass along that I really like the Owl bits, And for what it is worth, I would recommend that you try one.
Tom
|
|
|
Makita Cordless Router Collet |
Posted by: Bill Holt - 10-16-2024, 07:39 PM - Forum: Woodworking Power Tools
- Replies (3)
|
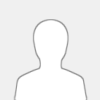 |
Love the router...not so happy with the "collet cone". Two maybe three times the router bit slipped down during operation. Now I get the nut so tight it is hard to loosen. Pluss...the cone is so tight, sometimes I have to remove it and push a tapered tool into the cone to expand the opening.
Today I found a tiny mark inside the router shaft and removed it with 600 sandpaper. I'm guessing there had been debris in there and that was the reason for the slipping bit.
All this to ask, has anyone else experienced a "tight collet cone"? I have five other routers (4 PC and 1 DeWalt) and have never had a problem.
|
|
|
Variable Speed Drive Upgrade to J/P |
Posted by: jteneyck - 10-16-2024, 08:08 AM - Forum: Woodworking Power Tools
- Replies (6)
|
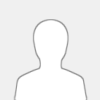 |
I had a thread on here a couple of weeks ago about why my MiniMax J/P bogged down taking off more than 1/32" on a 10" wide board. Folks here were helpful in helping to diagnose the problem. The solution was to either upgrade the 3 hp motor to something with more power or to slow down the speed of the feed rollers, currently about 26 fpm. After considering my options, I decided to implement a variable speed drive system for the feed rollers using a separate motor.
I did some torque calculations which suggested a motor like this one should work:
![[Image: AP1GczOLducd4Rw4Weep7PCg2piq0EilE4KKuuZ6...authuser=1]](https://lh3.googleusercontent.com/pw/AP1GczOLducd4Rw4Weep7PCg2piq0EilE4KKuuZ61_STn_YhK23RvKaDkGv9b8rC6opKEHyLCcUr9mhoE-TediJl8vv7HFsFjHVGoQZ6uzDwY2p0qaxk3na2ZoEAN04KQ9eziE1e8Of-ASzBiQ3rGSAZ3bhwcQ=w1705-h782-s-no?authuser=1)
The torque rating is comfortably more than what I thought I needed, and the speed range was good. There was just enough room in the cabinet of my J/P to install the motor. It's a tight fit because of the lift mechanism for the planer table. I made a template for the mounting holes of my mounting block and then drilled the holes. The cabinet is made with 3 mm steel which presented quite a challenge to drill through, lying down and on my side, especially the large hole for the shaft that carries the sprocket.
![[Image: AP1GczNE7l3D-gfP0sTNgUDfT0qcQSFqKOGeEAIb...authuser=1]](https://lh3.googleusercontent.com/pw/AP1GczNE7l3D-gfP0sTNgUDfT0qcQSFqKOGeEAIb2vmPPlaYKLjI55NMR0-A3o3PRHeotezXmWBKUq8KPiGIDQE2NdIQja_tUHh40epcy9y0sFyUI0lUoY9-uKemTmFhu7AR3Mg7Os1OcWWHKu3fJ5o3DQtd2A=w1565-h880-s-no?authuser=1)
The motor weighs over 15 lbs, which made it a bit of a struggle to get it installed, mating it to the flexible coupling between the motor and shaft and over the mounting bolts. But after the appropriate amount of cursing, I got it in place. I used my CNC to cut the various pieces of BB plywood I used to make the mounting block, which was very helpful. I glued and screwed the mounting block together. The motor seems very solid in the cabinet.
![[Image: AP1GczN2o_BKLjhXU9E_a0LRidb7CHRgwutxsneu...authuser=1]](https://lh3.googleusercontent.com/pw/AP1GczN2o_BKLjhXU9E_a0LRidb7CHRgwutxsneu6n7eyZC7imJcyaifD_bdYdbY7JnOt8lgSgmp72VOfpZQxHJTwxmuCim0AsP6NNFC4SSYvYgsYz28Vo3j2N5TDbmmqJMwDO5v_V-MC03V3-Mh08C6TliyBg=w1565-h880-s-no?authuser=1)
Looking down into the outer chamber of the cabinet you can see the sprocket the motor turns and chain. That's a 32 tooth sprocket driven by a #410 bicycle chain, the same as the original. The overkill 1" diameter shaft was necessitated by what parts I could find that were compatible. The motor has a 15 mm diameter shaft. I was lucky enough to find a 15 - 25 mm diameter coupler for it, so I used a 1" shaft and turned one end down to 25 mm to mate with the coupler. The sprocket was another adventure. I couldn't find a 1/8" sprocket with a 1" hub, so I ended up buying sprocket with a larger arbor hole and fitting it to a 1" hub. Anyway, it all worked out.
![[Image: AP1GczMC6zhxNselgwfaz1PqHHOe-u-hAoxNPdeK...authuser=1]](https://lh3.googleusercontent.com/pw/AP1GczMC6zhxNselgwfaz1PqHHOe-u-hAoxNPdeK6v5KIwnaZuFsUkV9tLxnwzyHRP82gNmkilUlxkSsIyGDGFJteizYSMcF6aAriY1SMZHpxiT5J_eZgLZssWvqbFoGW3QmtJchPFXraL3PTsjrNQ0AsrYqgw=w1565-h880-s-no?authuser=1)
Here's what the chain looks like now over the planer rollers:
![[Image: AP1GczNNCwJ3JKc1B88xZl-NuHxAUchHv1VDARI_...authuser=1]](https://lh3.googleusercontent.com/pw/AP1GczNNCwJ3JKc1B88xZl-NuHxAUchHv1VDARI_ozhn6cBdoH7HFMG82K0Lh_s4iwuL_LJOAXPX9xpem2rEYGhqyvtvR7klGpNHZs_5ifm3B6Pfnx09y5eMzYXtgOjFqFCWTni7kPH2UdHGc7cV2R6RTdtzAw=w1565-h880-s-no?authuser=1)
I was able to leave all of the original drive system in place, in case someone ever wants to convert it back. The sprocket on the right has a chain connected to the friction wheel, but it is now disconnected from the planer rollers, so all it would do is spin if I accidentally engage the friction roller.
The motor is controlled by a rheostat in a small box.
![[Image: AP1GczPZlmMIFAkegxYDFrAlwojTr6wlkEBIMBFC...authuser=1]](https://lh3.googleusercontent.com/pw/AP1GczPZlmMIFAkegxYDFrAlwojTr6wlkEBIMBFCOYeog92xcST-_XMkox07oPwGrGs2xLYQKm1ISVtvQBKLRSr1_p_U0rTEXXlo8cj1-7lV7P_PPbQTYgYsPa2VuuKHIgcCstbYlICNBclK0lrKxnXV4-oeRg=w1565-h880-s-no?authuser=1)
I mounted it in the outer casing at the infeed side of the planer. It looks like it belongs there.
![[Image: AP1GczMWffdIOfL1yc_C2IgO1oyvXlwL3OH-TJLM...authuser=1]](https://lh3.googleusercontent.com/pw/AP1GczMWffdIOfL1yc_C2IgO1oyvXlwL3OH-TJLM7-Lp5LVukvojler9BQ0Et4fRrv2HcynNTbUFKkcrJFZAAK0RY-IRQkP6NBLP8qePZboPDOD5Psl-v2lcY1UIsGsCCIjoXb8Ac5YWSx6yiOLMOSdl3fjEbw=w495-h880-s-no?authuser=1)
That completed the installation. I still have to tidy up the power cables inside the casing, but I did a test run with it to see if/how it works. Maximum speed is now 22.5 fpm. At that speed the motor had no trouble taking off a 3/32" bite on the same 10" board it used to struggle at 26 fpm to take off 1/32", and the new variable speed drive motor pulled the board through the planer with no issue. I'd call it a success. I haven't tried it at lower speeds yet, but I'm pretty sure that if I run it in the 15 fpm range I'll be able to run a Byrd head in it w/o over taxing the main motor. The further benefit will be that even with the current cutterhead, I'll be able to take fewer passes and improve cut quality by slowing down the feed. I'd call it a win-win.
John
|
|
|
Knife Display Case |
Posted by: BrokenOlMarine - 10-15-2024, 11:54 PM - Forum: Woodworking
- Replies (41)
|
 |
I have been making knives for a while now, but not for sale. I make them for myself, Miss Tina, or for friends and family. NOW, I am running out of things to do with them, and I don't sell them so they are piling up. Tina told me I need to make a display case and get them of the table in the entry area. Two concerns... a kid could pick one up and they are RAZOR sharp. Secondly, someone we don't know well could palm one on the way out the door. (Service Person of some sort..) There goes $350 to $1,000 retail value if I was selling them, out the door. Right now there are a dozen on that table.
So, a couple months ago, I started thinking about the display case. HER suggestion was wall mounted, above the table. Move the picture and get rid of the lamp. I started designs, and tossed them. Started designs, and tossed them. Eventually, I settled on 48" wide, same width as the table... and 16" high. Then it was a matter of choosing the wood and the actual layout of the construction. I was shocked at the cost of the project. Wood, finished oak and birch at Home Depot has gotten dear. I searched through my woodpile and came up with some walnut. That meant it would go thru the planer and get Ripped to size then cut.
|
|
|
|